After more than a year and a half's work, we are pleased to announce the launch of our first model equipped with a sole made from old, recycled Benjie shoes. It's a minor achievement given the scale of today's climate change challenge, but it's a major step forward in terms of recycling, and fundamental to our understanding of the issues involved.
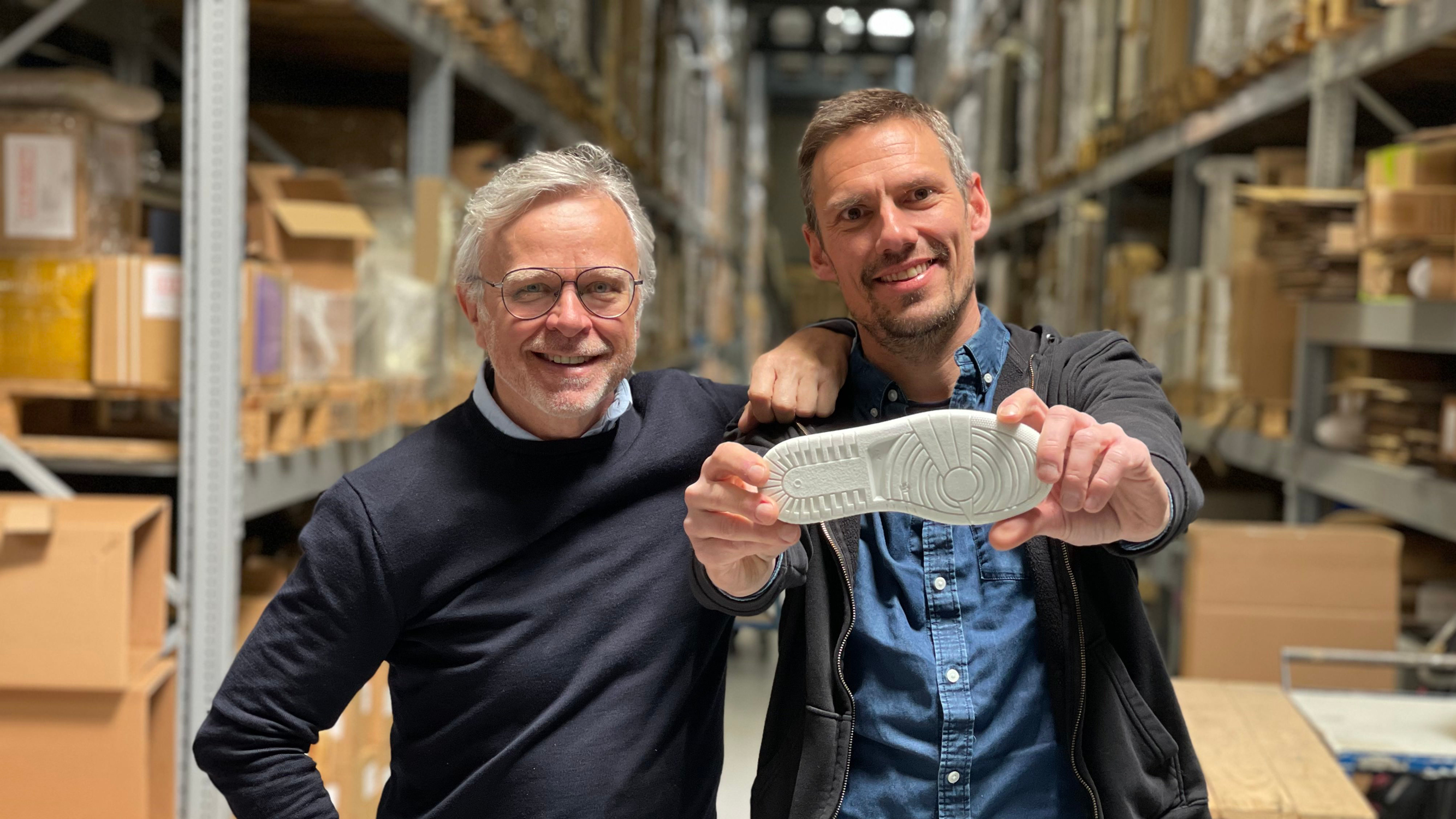
We tried to get around the problem by taking waste as raw material. If it is currently impossible to create a new shoe that is entirely recycled, why not focus on just one part of it? And it's the sole that we've turned our attention to. By including some waste in the sole's paste, we found a way to recycle.
To carry out such a project, we had to make specific sole moulds and do a lot of research. For a small company like ours, it was difficult to invest, which is why we launched a crowdfunding campaign in June 2022 that enabled us to raise nearly CHF 34,000!
Thanks to you, we were able to manufacture the moulds for the new recycled soles.
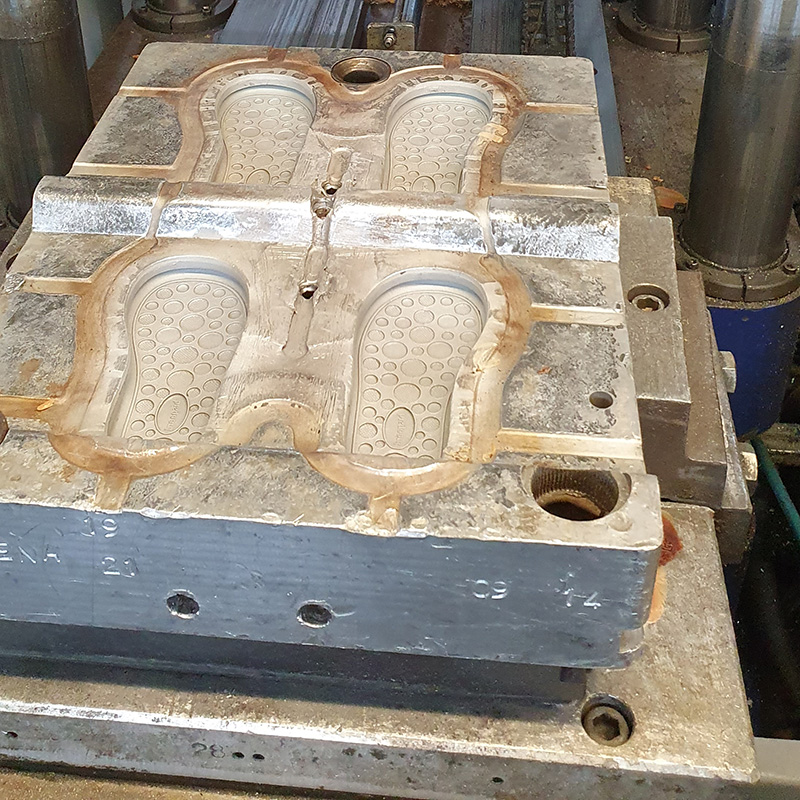
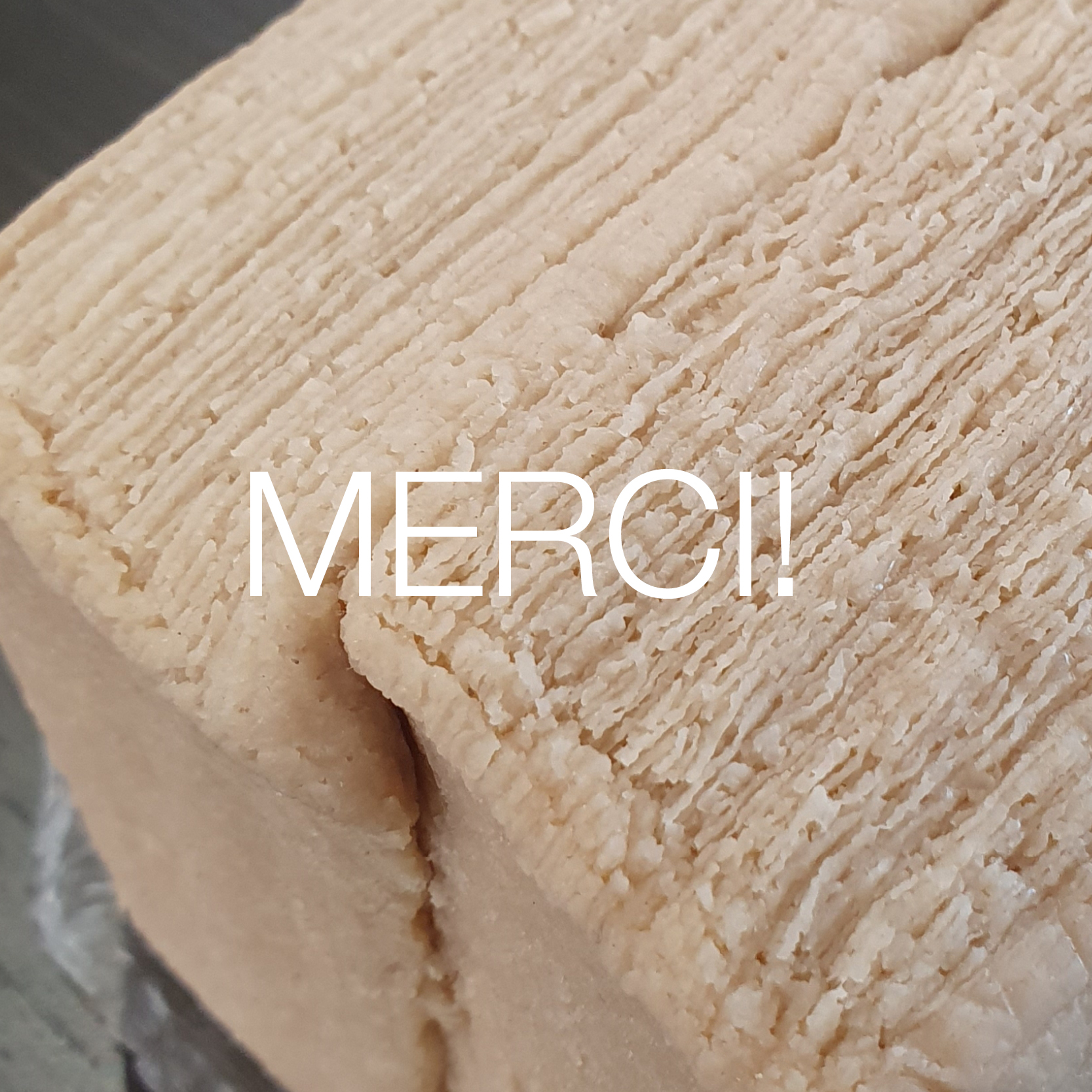
All the steps involved in turning a used shoe into a new one
From collecting used Benjie shoes to returning them to Portugal and manufacturing the soles for the final shoe, here's every step of a complex process where everyone plays a role: consumer, brand, logistics partner, and factory.
THE RAW MATERIAL
Collecting used shoes
Every day, you bring us your used Benjie shoes. Our aim is to stimulate a new consumer reflex to recycle.
Back to Portugal
Once sorted, shoes that can be repaired are donated to the Caritas / CSP Genève social cloakroom. Severely damaged shoes are sent back to Portugal together with new deliveries to avoid empty returns.
Ingredients
Crushed Benjie powder + recycled natural rubber + recycled synthetic rubber create a robust, high-quality sole.
Crushed Benjies: All parts except metal are ground into powder in Portugal.
Recycled natural rubber: Mixed with crushed Benjie powder to regain elasticity and resistance.
Recycled synthetic rubber: Added for lightness and to avoid consuming new raw materials.
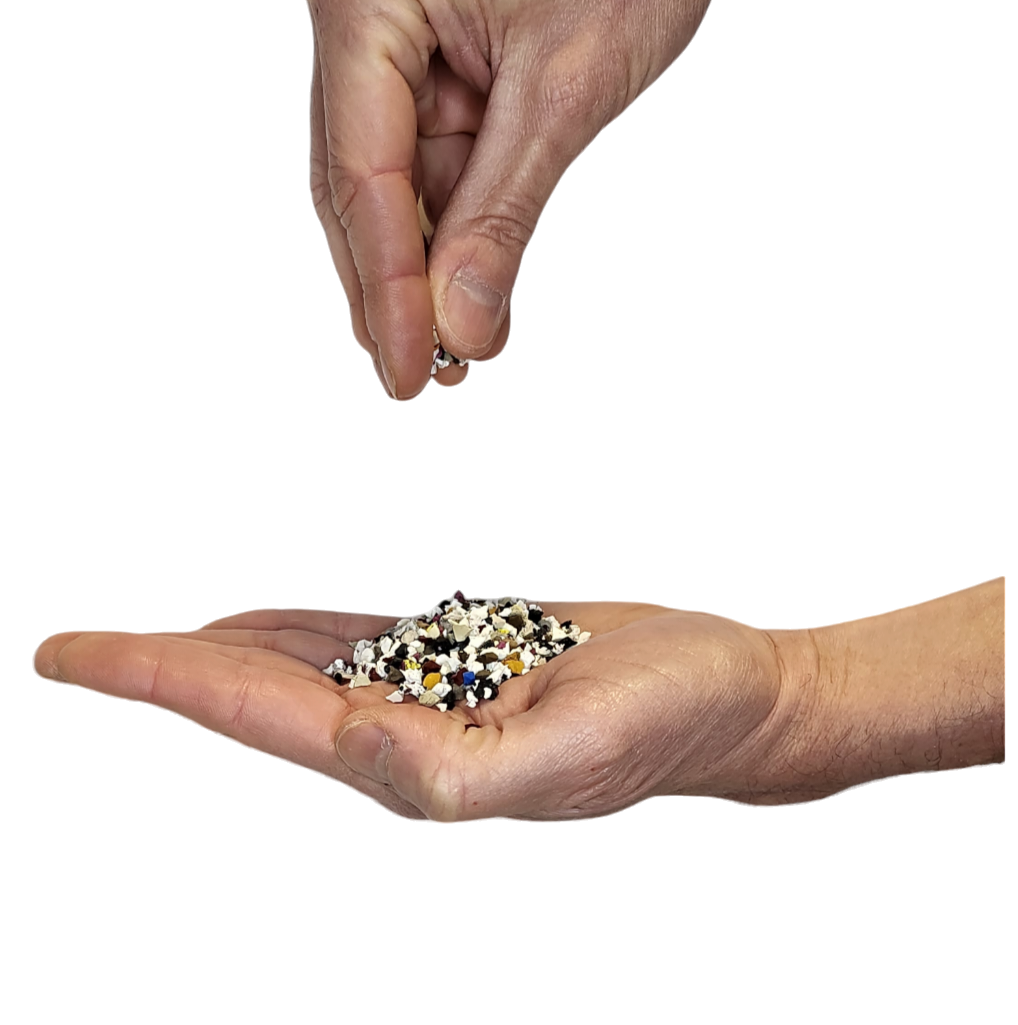
THE RECYCLED SOLE
The mixture is injected into moulds at high temperature and complies with EU anti-toxicity standards.
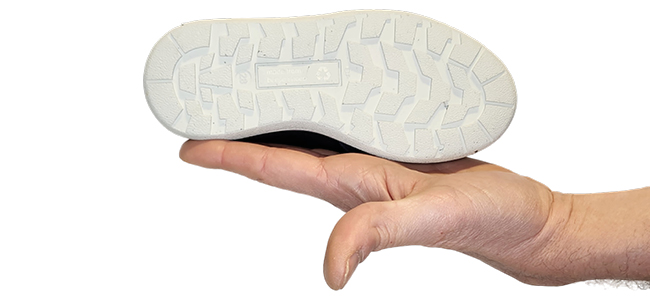
TWO CERTIFICATIONS
- Global Recycling Standard
- RCS 100 Recycled Claim Standard
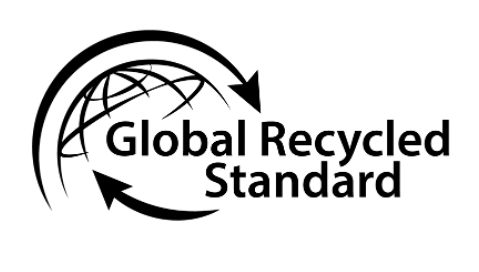
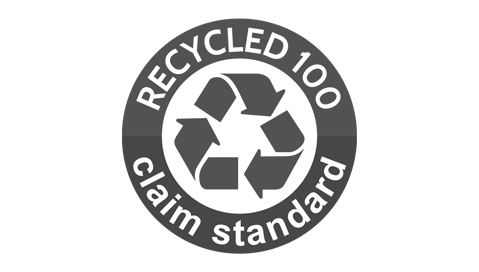
LIMITATIONS AND FUTURE PROSPECTS
While significant, we still incorporate other recycled materials for strength, limiting full circularity. Achieving 100% recycling requires completely reinventing shoe design. Nonetheless, customer participation has shown that recycling practices can become routine.
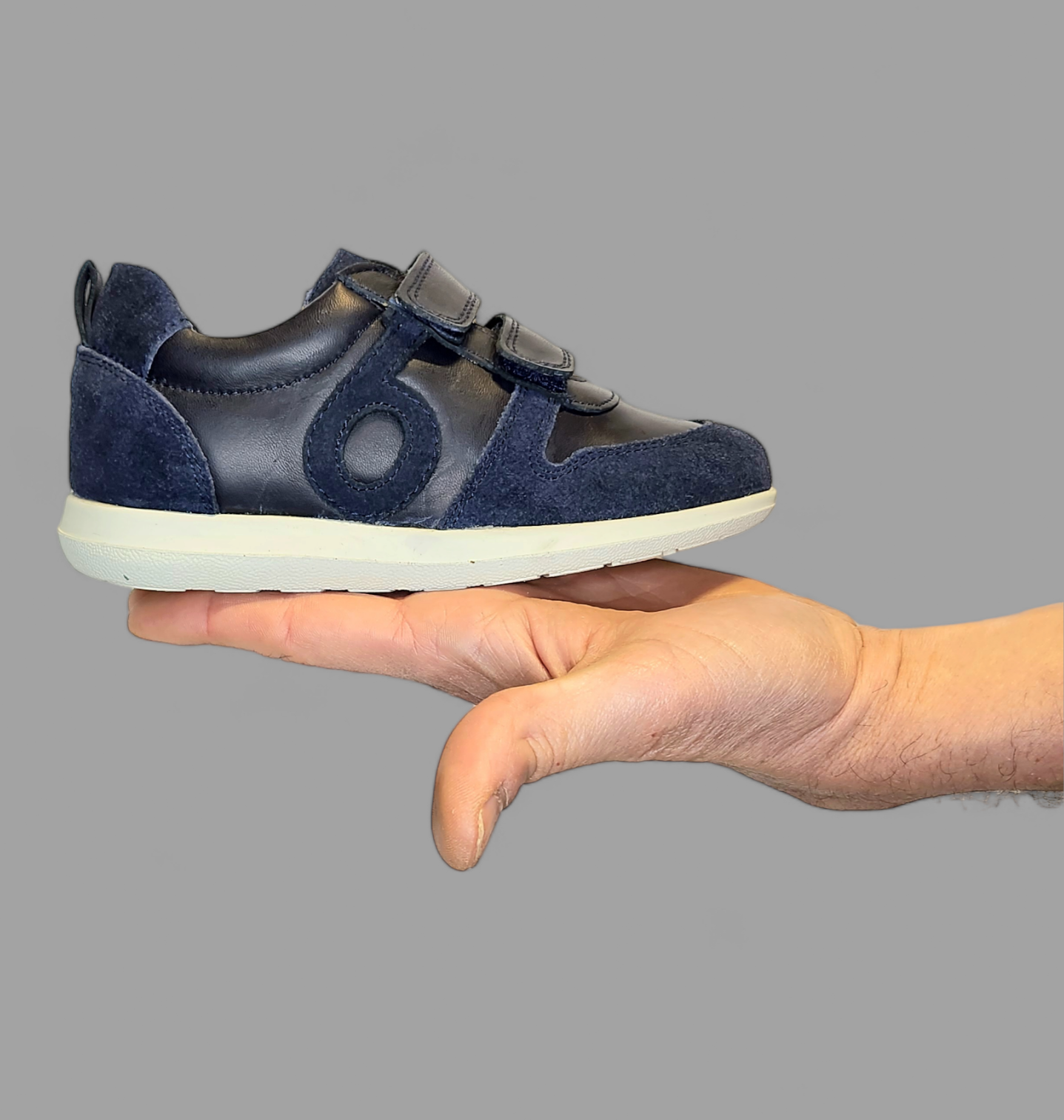